INNOVATIVE SENSOR SOLUTIONS
Understanding the pivotal role of accurate temperature measurement in your processes, we offer an expansive portfolio of industrial sensors. For environments above 1200°C such as incinerators, we offer Thermowells with specialised materials like metal sheaths and ceramic. Custom orders for unique materials are welcome.
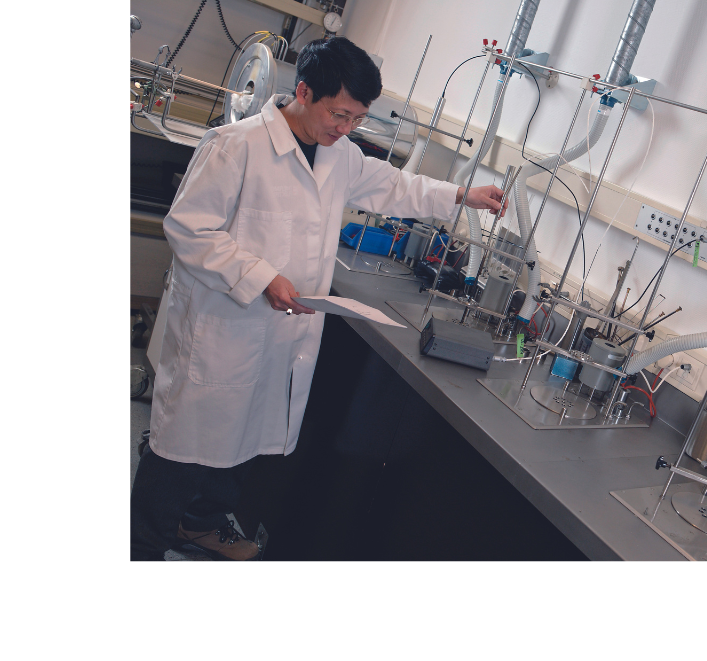
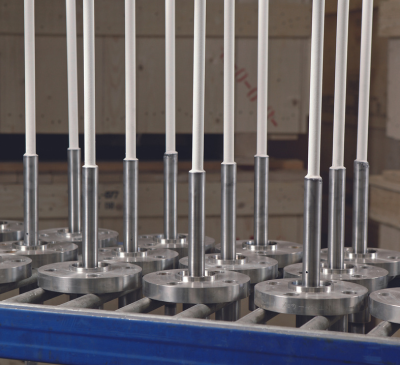
MULTIPLE TYPES
From single to duplex thermocouples and 2 to 4-wire RTDs, our sensors are designed to meet your needs.
INDUSTRIAL SENSORS
Our thermocouples and RTDs are available in both single and duplex configurations.
THERMOWELL OPTIONS
Select from fabricated or solid Thermowells with flanged or screwed connections, that are rigorously tested.
CERTIFICATIONS
Our products meet the stringent requirements of multiple certifications including ATEX, IEC/ex, and CSA/us.
what our customers say
"Thermo Electric Instrumentation is the go-to company for temperature measurement systems. Their products are reliable, durable, and of the highest quality. We have used their solutions for our chemical plant, and they have consistently outperformed other sensors in the field."
John Regan
Chemical Plant Manager“We have been working with Thermo Electric for several years now and have always been impressed by their knowledgeable and experienced workforce. Their ability to seamlessly integrate with our main contractors has made working together a breeze.”
Sarah Trebaut
Project Manager for Engineering Company“Thermo Electric's spike and profile thermocouples are a game-changer. Their unique features and benefits, such as improved positioning of measurement points, ensure greater accuracy in Delta T measurements. Their extraordinary care and calibration provide peace of mind that every sensor is manufactured to the highest degree of quality”
Michael Chen
Procurement Specialist“We have been using Thermo Electric's temperature sensors in our steel mill for years and have found them to be of the highest quality. Their ability to provide innovative solutions to high-temperature measuring requirements has been invaluable, and their platinum sleeved thermocouple sensor has resulted in significant cost savings.”
David Williams
Steel Mill Operations Manager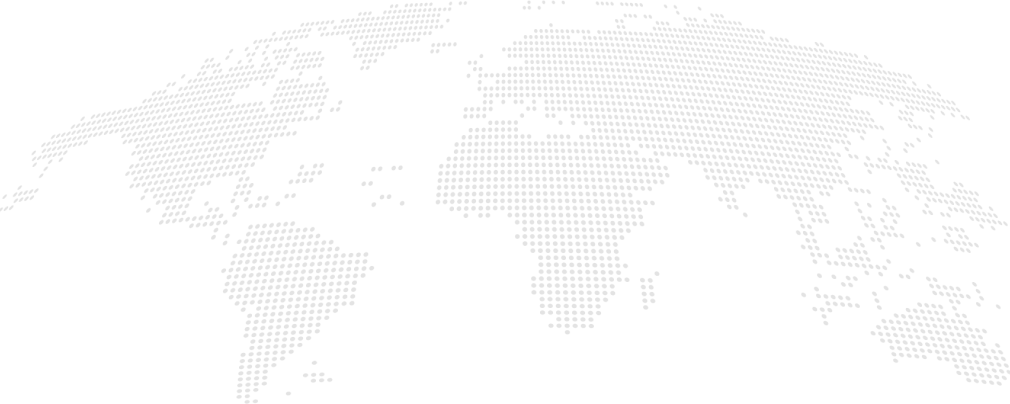
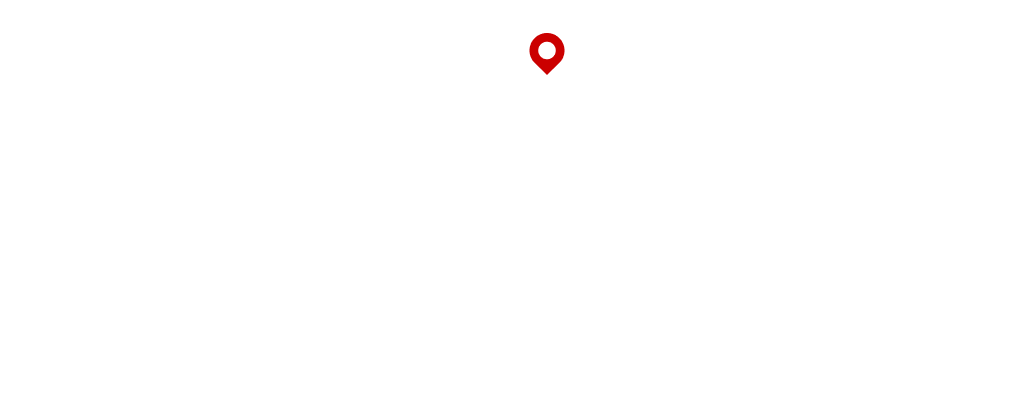
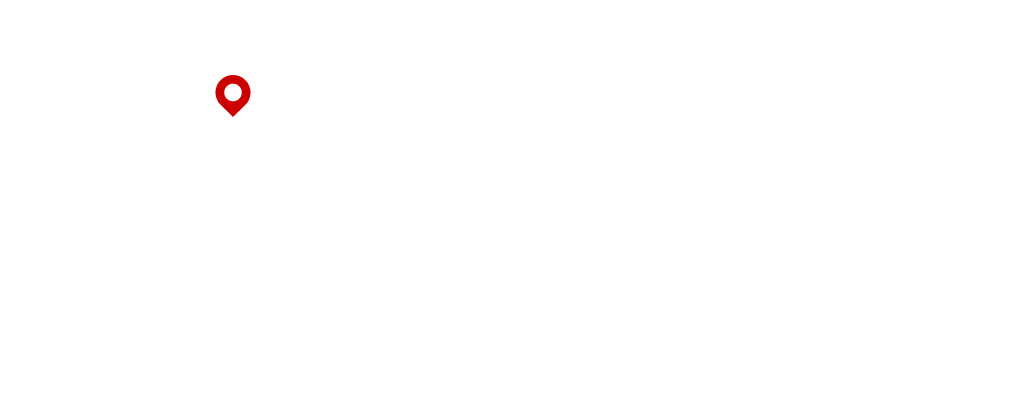
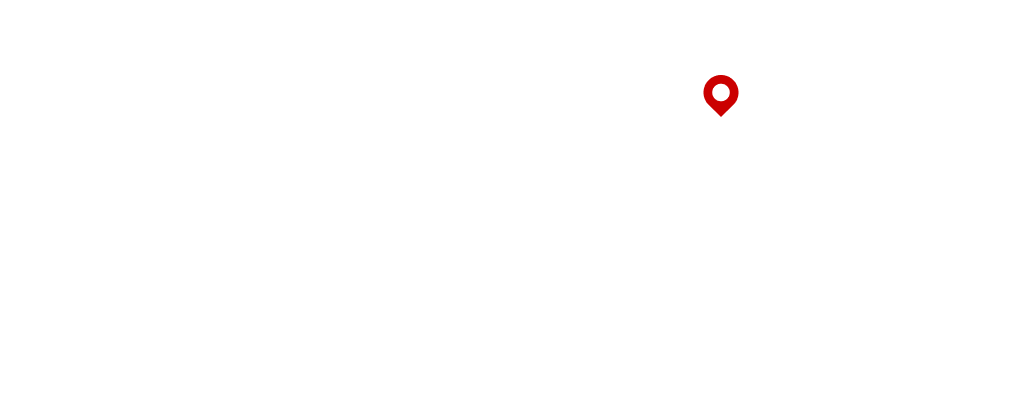
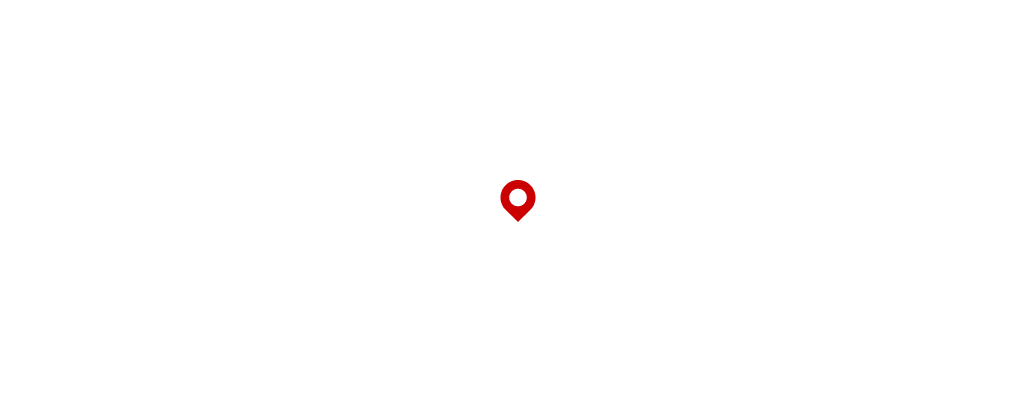
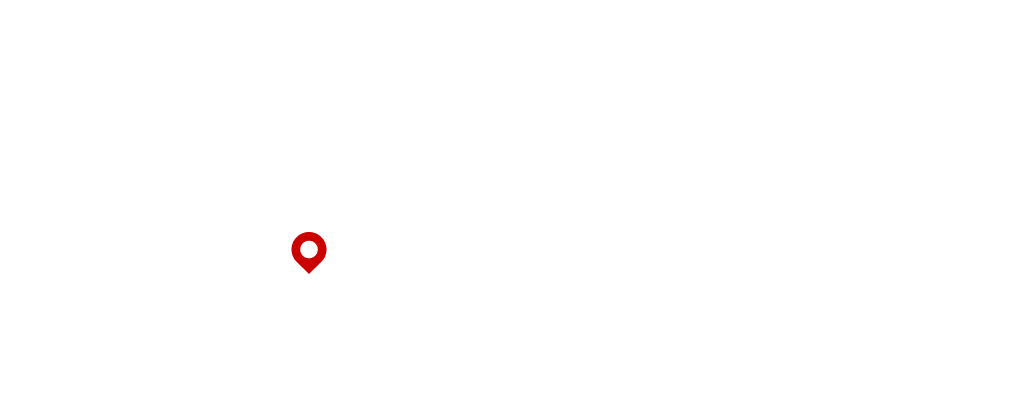