ENHANCING RELIABILITY IN ETHYLENE CRACKER FURNACES
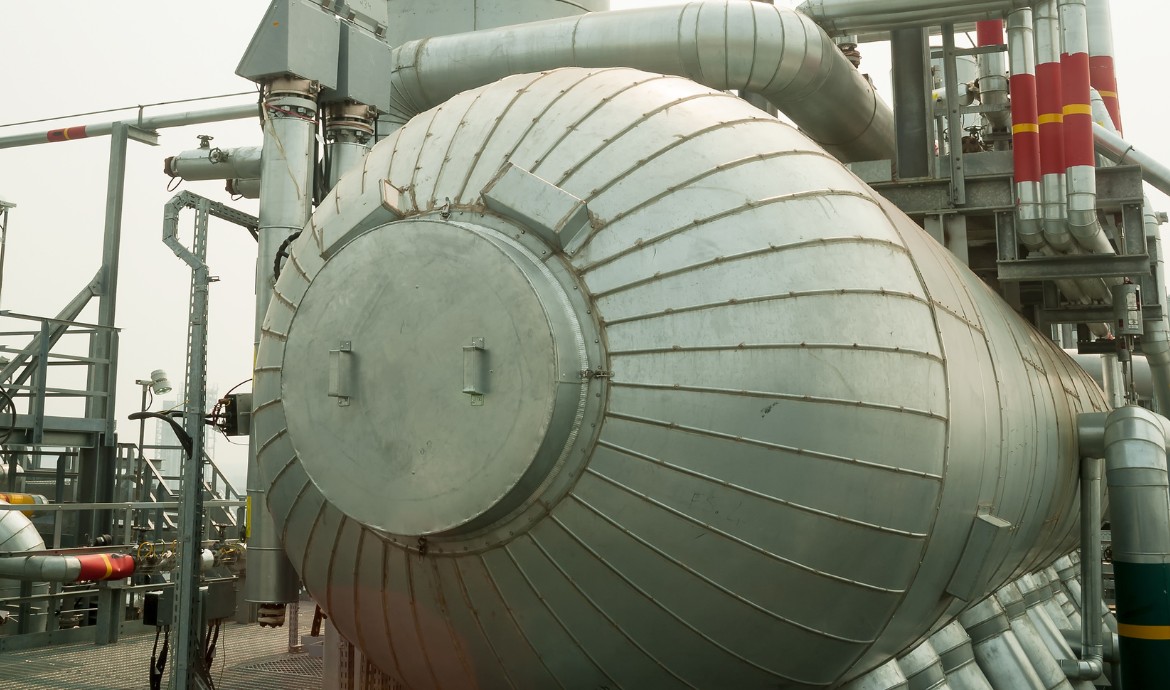
CATEGORY: Ethylene Production
PRODUCTS: Industrial Assemblies
DATE: April, 2022
Background
The ethylene production industry is characterised by an intense focus on efficiency and reliability, given the highly competitive market and the complex nature of the production process. In this challenging environment, the ethylene cracker furnaces are the heart of the operation, responsible for breaking down hydrocarbon feedstocks into simpler compounds, including ethylene. A slight deviation in temperature or pressure can severely affect the yield and quality of the produced ethylene, leading to financial losses and safety concerns. For one particular plant, these challenges were exacerbated by frequent thermocouple failures and drift in their cracking furnace effluent streams. These issues not only disrupted the plant’s daily operations but also led to increased maintenance costs and downtime. Given the highly reactive and extreme environment within the furnaces, temperature sensors needed to not only be accurate but also extraordinarily resilient. It was clear that a more robust and reliable solution was needed to address these pressing issues, setting the stage for a project that would call upon cutting-edge engineering and tailored service solutions.
SOLUTION
Confronted with the problem of frequent thermocouple failures and drift, the plant faced multiple operational hurdles. Traditional type K thermocouples would only last a few months before breaking or drifting beyond usable accuracy. The unreliability of these sensors led to imprecise process control, compelling the plant to initiate unplanned decoking outages to replace the failed sensors. These unscheduled interruptions not only incurred significant maintenance costs but also compromised the quality and consistency of the ethylene output.
In response to these pressing issues, an external vendor was engaged to introduce an advanced solution. Leveraging their expertise in proprietary materials and construction, they provided an upgraded version of the type K thermocouples. This enhanced design was specifically engineered to provide better stability at the high temperatures commonly found in ethylene cracker furnaces. Additionally, new thermowells were developed, constructed from alloys and designed with geometries capable of withstanding the extreme conditions within the cracking environment.
Through this strategic collaboration, the plant successfully replaced its failing temperature sensors with more robust and reliable alternatives. The upgraded thermocouples delivered a five-fold increase in furnace runtimes before requiring replacement, marking a significant advancement in reliability and efficiency for the plant.
Customised Services
In order to meet the unique requirements and challenges faced by the ethylene production facility, a personalised approach was adopted from the very first point of contact. Our dedicated team of specialists engaged in detailed consultations with the client to understand the specific operational issues they were facing. This allowed us to tailor our solutions to directly address these challenges. Throughout the implementation process, the customer was continually updated, ensuring that the solutions provided were not only technically sound but also aligned closely with their operational needs and timelines.
ENGINEERING EXCELLENCE
A cornerstone of this project's success was our commitment to engineering excellence. Our team utilised state-of-the-art design software and simulation tools to ensure the robustness and reliability of the upgraded thermocouples and thermowells. Our expertise in material science enabled us to select alloys that would withstand extreme temperatures and harsh operational conditions. Furthermore, each component underwent rigorous testing to verify its durability and performance, ensuring that it met or exceeded industry standards as well as client expectations.
RESULTS
The introduction of the upgraded thermocouples and newly-engineered thermowells had a profound impact on various facets of the plant’s operations. Here are the notable outcomes:
- Extended Sensor Life: The revamped thermocouples, designed to withstand the harsh conditions of the cracker furnaces, increased the sensors’ lifespans by up to five times compared to the previous models. This extension substantially reduced the frequency of unplanned decoking and sensor replacement outages.
- Improved Operational Efficiency: With sensors that maintained their accuracy over a longer period, the plant enjoyed enhanced process control. This improvement allowed for the optimisation of feed balances and led to a decrease in coking rates, thereby increasing the overall operational efficiency.
- Cost Savings: The longer lifespans of the new thermocouples meant fewer replacements were needed, leading to significant savings on part costs and labour. These savings were further amplified by the reduction in downtime and lost production opportunities.
- Enhanced Data Accuracy: The new thermocouples provided more reliable and precise temperature measurements. This data accuracy enabled the plant’s control systems to make more effective real-time adjustments to the cracking process, thereby optimising product quality and yield.
- Safety and Compliance: With more reliable temperature monitoring, the plant could ensure safer operating conditions and better compliance with industrial safety standards. This not only minimised the risk of accidents but also could potentially reduce insurance costs.
- Environmental Benefits: More efficient operation and reduced coking rates also contributed to a decrease in waste and emissions, aligning the plant more closely with environmental regulations and sustainability goals.
- Competitive Advantage: The combined benefits of increased efficiency, reliability, and safety gave the plant a significant edge over competitors still grappling with sensor reliability issues.
- ROI and Future Scalability: The initial investment in upgrading the thermocouples and thermowells was rapidly recouped through increased production and reduced operational costs. The success of this project also opened the door for similar upgrades in other parts of the plant, promising additional future benefits.
In summary, our partnership with the engineering contractors in upgrading the thermocouples and thermowells not only solved immediate challenges but also provided a foundation for ongoing improvements in operational efficiency, cost-effectiveness, and environmental compliance.